Additive manufacturing of magnetocaloric heat exchangers for hydrogen liquefaction
Advanced Research Lab, Master Thesis
The liquefaction of hydrogen is crucial for the adoption of clean hydrogen energy, as it significantly increases storage density and simplifies transportation. However, the liquefaction process requires a significant amount of energy and accounts for approximately one-third of the cost of liquid hydrogen. The use of solid-state magnetocaloric cooling can improve the energy efficiency of hydrogen liquefaction.
Magnetocaloric cooling relies on magnetic materials, such as Holmium. The materials exhibit an entropy or adiabatic temperature change when exposed to a magnetic field. This reversible adiabatic temperature change can be utilized in repeated magnetization and demagnetization steps to transfer heat and progressively lower the temperature below the liquefaction point of hydrogen (20 K).
To enable good heat transfer, porous structures with a high surface-to-volume ratio are required to reach high cooling power. Additive manufacturing techniques, such as laser beam powder bed fusion (PBF-LB), enable the processing of highly complex heat exchanger geometries.
In this work, we offer a study on the PBF-LB processing of Holmium for magnetocaloric heat exchangers. The study includes a parameter analysis to determine the optimal processing parameters for Holmium and subsequent parameter optimization for heat-exchanger geometry. Besides the synthesis, the work also consists of the structural, microstructural, and magnetic characterization of the processed part.
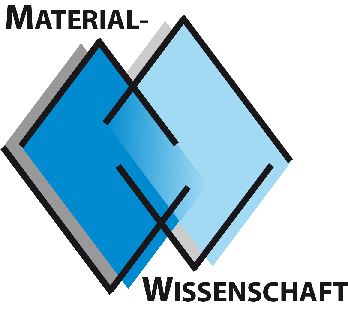