Recycling Magnets
“MagCycleAM” project funded by Volkswagen Foundation with around 1.1 million euros
2025/04/02
The Volkswagen Foundation has approved new projects in the "Circularity with recycled and biogenic resources" funding initiative: For four years and with around 1.1 million euros, the project "MagCycleAM – Resource and Energy Efficient Recycling and Additive Manufacturing of Nd-Fe-B Magnets", led by Professor Oliver Gutfleisch, will be funded. In cooperation with the Fraunhofer Research Institution for Materials Recycling and Resource Strategies IWKS Hanau and The Weizmann Institute of Science in Rehovot, a team is researching the production of sustainable permanent magnets.
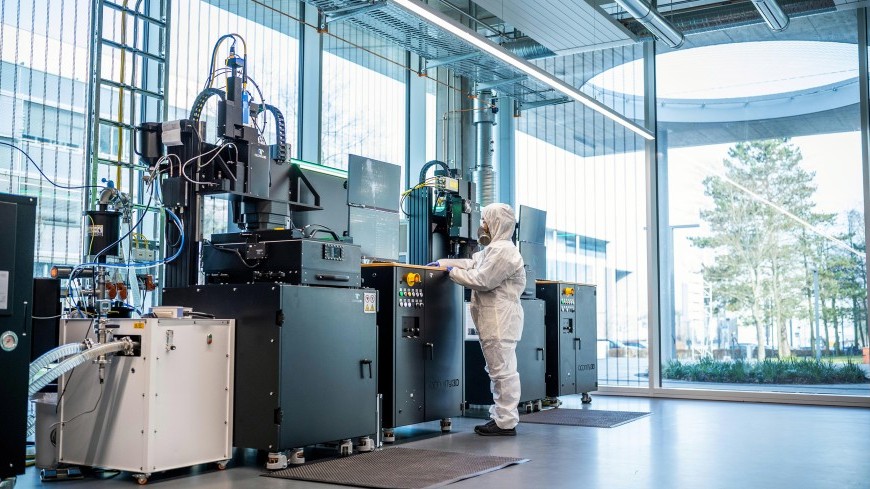
In this project, we represent a strong consortium with many years of experience in magnet production and development, which aims to realize an innovative approach to sustainable powder and magnet production.
Professor Oliver Gutfleisch
A wide array of high-performance magnets is currently available, exhibiting significant variations depending on their application and manufacturer. These magnets find diverse applications, including those in the fields of electromobility and wind energy. The technical feasibility of direct reuse of Nd-Fe-B-based magnets (permanent magnets) from old electric motors is evident, as the magnetic properties of the magnets remain unimpeded by operation. However, the lack of standardization among these magnets hinders their practical implementation. The consortium's objective is to facilitate the recycling of these magnets for subsequent reuse. However, the chemical elements are not separated from each other and placed on the market as rare earth oxides, for example, but are processed into powder by hydrogen atomization or rapid solidification of the melt. This processed powder can be reused for magnet production. Achieving these objectives necessitates a reduction in energy consumption, thereby minimizing CO2 emissions and waste generation. This can be accomplished without resorting to the use of environmentally harmful chemicals. To further reduce energy consumption and material waste, additive manufacturing of Nd-Fe-B magnets is a promising approach for a sustainable and efficient production chain and a comprehensive material cycle. This approach offers distinct advantages over conventional sintering or hot forming of magnets, including enhanced geometric freedom in magnet design, which optimizes applications such as electric motors. Consequently, the project integrates recycling with additive manufacturing technology to produce sustainable (“responsible”) permanent magnets.
We benefit from the excellent infrastructure and the know-how of our TU Darmstadt partners at the Additive Manufacturing Center (AMC).
Dr. Lukas Schäfer from the AMC
535,800 euros of the funding will go to TU Darmstadt. is in charge of this project and is working on additive magnet production, more specifically on the optimization and characterization of magnetic properties. This project specifically uses the PBF-LB/M method for processing recycled magnetic materials, which has not yet played a commercial role. The main feature of this technique is that no binder phase is used, which means that the powder material is processed into fully dense parts by re-melting. This is the only way to achieve the same high performance as sintered magnets. This process must be controlled, e.g. to prevent the formation of secondary phases (especially soft magnetic iron), but also to produce an optimal grain size and texture. The current magnetic performance of such “printed” magnets cannot yet compete with the energy products of commercial Nd-Fe-B magnets. However, this process offers significant advantages through energy-efficient processing, minimal material waste and geometric freedom in contrast to conventional manufacturing processes. The “Functional Materials” research group
Building on previous research
TU Darmstadt has already gained valuable experience in the field of additive manufacturing of magnetic materials as part of the coordinated by Professor Gutfleisch. Collaborative Research Center CRC/TRR 270
In addition, significant progress has been made in process optimization and material characterization within the at TU Darmstadt – in particular through successful collaboration with the Mechanical Engineering Institute for Production Management, Technology and Machine Tools Additive Manufacturing Center. This collaboration led to a project “QuamM – Qualification of magnetic materials for additive manufacturing”, funded by the Forum for Interdisciplinary Research ( PTW). FiF
The funding initiative
The new projects approved by the Volkswagen Foundation represent practical research approaches that aim to achieve closed raw material-product cycles. Avoiding or recycling waste are important steps towards new production technologies that cost less but are more efficient and environmentally friendly. The exploitation of its primary raw materials is pushing the “system Earth” to its limits. Greenhouse gas emissions, biodiversity loss and water consumption are also continuing to increase. The circular economy or “circularity” can point the way out of this spiral of deficits. This is why the Volkswagen Foundation is funding this important and promising field of practical research.
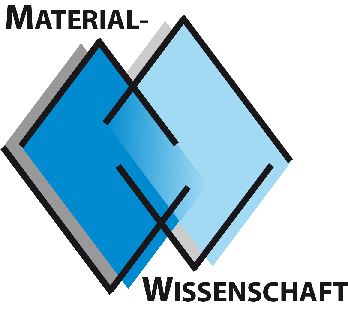