A thermo-mechanical phase-field fracture model: application to hot cracking simulations in additive manufacturing
New Publication in “Engineering Structures”
2022/12/14

Authors: Hui Ruan, Shahed Rezaei, Yangyiwei Yang, Dietmar Gross, Bai-Xiang Xu
Thermal fracture is prevalent in many engineering problems and is one of the most devastating defects in metal additive manufacturing. Due to the interactive underlying physics involved, the computational simulation of such a process is challenging. In this work, we propose a thermo-mechanical phase-field fracture model, which is based on a thermodynamically consistent derivation. The influence of different coupling terms such as damage-informed thermomechanics and heat conduction and temperature-dependent fracture properties, as well as different phase-field fracture formulations, are discussed. The model is numerically implemented with the finite element method. Finally, the model is applied to simulate the hot cracking in additive manufacturing. Thereby not only the thermal strain but also the solidification shrinkage is considered. As for the thermal profile, both analytical temperature solution and numerical thermal field around the melting pool are taken into account. Based on the latter approach, the influence of different process parameters is further studied. The study reveals that the solidification shrinkage strain takes a dominant role in the formation of the circumferential crack, while the temperature gradient is mostly responsible for the central crack. Process parameter study demonstrates further that a higher laser power and slower scanning speed are favorable for keyhole mode hot cracking while a lower laser power and quicker scanning speed tend to form the conduction mode cracking. The numerical predictions of the hot cracking patterns are in good agreement with similar experimental observations, showing the capability of the model for further studies.
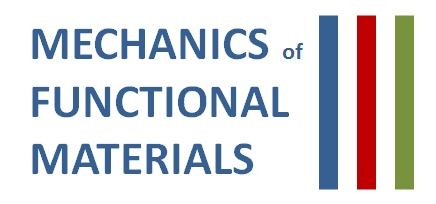