Large-Scale Interlaboratory Study Along the Entire Process Chain of Laser Powder Bed Fusion: Bridging Variability, Standards, and Optimization across Metals and Polymers
New Publication in “Advanced Engineering Materials”
2025/06/17
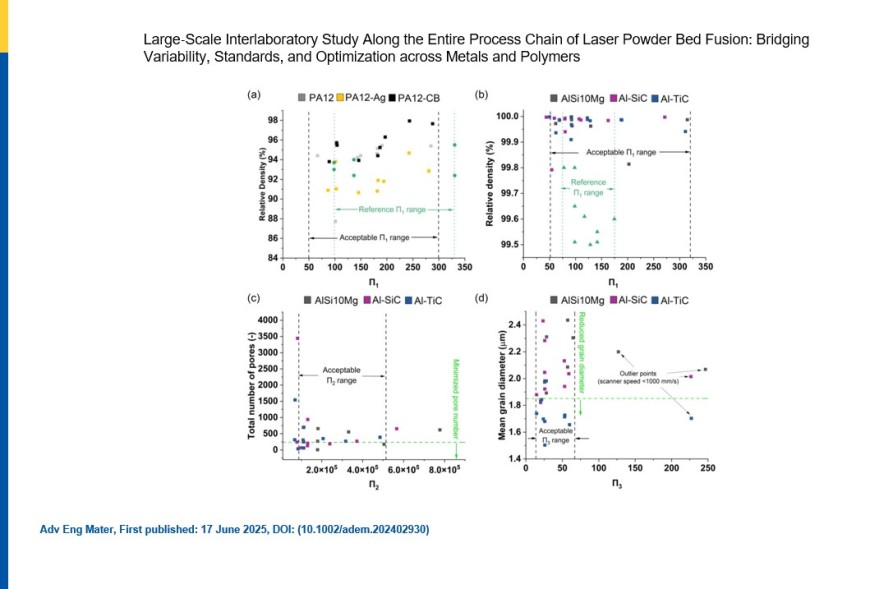
Authors: Ihsan Murat Kuşoğlu, Sunidhi Garg, Arvid Abel, Prasanna V. Balachandran, Stephan Barcikowski, Louis Becker, Jan-Simeon Bernsmann, Jonas Boseila, Christoph Broeckmann, Mert Coskun, Malte Dreyer, Mark East, Mark Easton, Nils Ellendt, Stan Gann, Bilal Gökce, Mareen Goßling, Joachim Greiner, Piotr Gruber, Moritz Grünewald, Kopila Gurung, Nick Hantke, Florian Hengsbach, Hannes Holländer, Brecht Van Hooreweder, Kay-Peter Hoyer, Yajiang Huang, Florian Huber, Olaf Kessler, Burçin Özbay Kısasöz, Stefan Kleszczynski, Ebubekir Koc, Tomasz Kurzynowski, Arno Kwade, Simon Leupold, Dongmei Liu, Felix Lomo, Arne Lüddecke, Gerrit A. Luinstra, David A. Mauchline, Fabian Meyer, Lars Meyer, Peter Middendorf, Stefan Nolte, Michał Olejarczyk, Ludger Overmeyer, Andrij Pich, Sebastian Platt, Felix Radtke, Roland Ramm, Silja-Katharina Rittinghaus, Richard Rothfelder, Johannes Rudloff, Mirko Schaper, Marie Luise Scheck, Johannes Henrich Schleifenbaum, Michael Schmidt, Jan T. Sehrt, Yvonne P. Shabanga, Alexander Sommereyns, Rabea Steuer, Layla Shams Tisha, Anastasiya Toenjes, Christopher Tuck, Adrian Vaghar, Bey Vrancken, Zhengze Wang, Sebastian Weber, Jan Wegner, Bai-Xiang Xu, Yangyiwei Yang, Duyao Zhang, Evgeny Zhuravlev, Anna R. Ziefuss
Laser powder bed fusion is a cornerstone technology for additive manufacturing (AM) of metals and polymers, yet challenges in achieving consistent reproducibility and process optimization persist. Addressing these requires a systematic understanding of the interactions between feedstock, process parameters, and final part characteristics throughout the entire production chain. This study presents results from a comprehensive interlaboratory investigation conducted by 32 research institutions, evaluating six feedstock, including nanoparticle-modified aluminum alloy and polyamide powders, under standardized protocols. Data analysis encompasses 69 powder properties, 15 process parameters per print, and 78 part features, culminating in a dataset of over 1.2 million correlations. Advanced statistical methods and machine learning are employed to identify critical variability drivers, such as the impact of nanoparticle modifications on powder flowability and thermal conductivity, as well as the influence of process parameters on reproducibility. Newly introduced dimensionless figures of merit provide universal metrics to describe and predict thermal and mechanical interactions, simplifying process optimization and material characterization. The findings, supported by an open-access dataset adhering to findable, accessible, interoperable, and reusable principles, advance understanding of material–process–structure–property relationships. They establish a benchmark for future research and lay the foundation for improving the reliability, quality, and sustainability of AM processes.
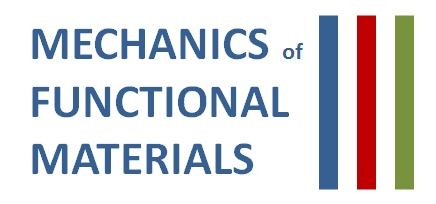